Quality management in scaffolding construction
An overview of the quality management processes
- Home
- >
- Scaffolding
- >
- Scaffolding quality management
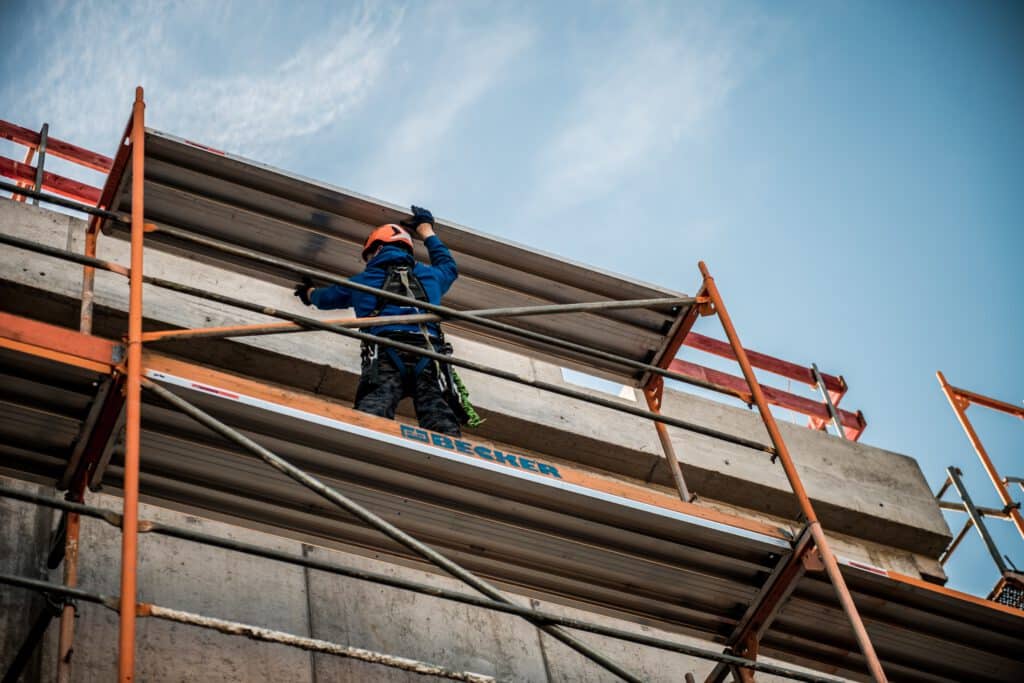
Quality management in the scaffolding trade: a decisive factor that is often underestimated. Outdated quality standards and inconsistent controls can not only affect the end result, but also pose safety risks.
Imagine a construction site where every scaffolding component, every connection and every assembly step meets the highest quality requirements.
Sebastian Waack understands the special challenges of the scaffolding trade and has the know-how to raise quality standards to a new level.
Targeted quality management reduces defects, increases the quality of work and minimizes potential risks. Imagine that every step of the process is carried out with precision and care and you can be sure that every project will meet the highest standards. More security, higher customer satisfaction.
Are you ready to revolutionize the quality of your craft?
Improvements through quality management:
Standardization expert:
Sebastian Waack assisted a Hamburg-based scaffolding company in clarifying spongy working procedures by setting precise digital standards for quality work.
Surveillance guru:
Sebastian introduced a digital monitoring system at a scaffolding company in Düsseldorf that constantly checks the quality of work so that defects are detected and addressed immediately.
Proofreading professional:
Sebastian developed and implemented a digital process for a Leipzig-based company to ensure that quality problems are not only rectified, but also avoided in the future.
- Process documentation
- Digitization
- Inventory Management
- Employee development
- Quality management
Example solutions for quality management in the scaffolding trade
Documentation revolution in the scaffolding trade:
Clear overview in scaffolding construction:
Sometimes scaffolders don’t know exactly how best to do their work because the instructions are missing or difficult to find.
Sebastian Waack has a simple solution. He brings a computer program with him where all the important information is stored. Anyone can quickly check what needs to be done – whether in the office or out on the building site.
Sebastian shows everyone how to use the program so that everyone can make good use of it. This means that the scaffolders can work better and there are fewer errors. That’s good for everyone!
Stable scaffolding construction is based on detailed quality standards and clearly defined processes. However, these are often only handed down orally or hidden in physical files, which can lead to ambiguities and errors in the workflow.
Sebastian Waack has an innovative solution for exactly this. He introduces digital documentation systems in which all quality standards and work processes are centralized, organized and always kept up to date. This gives employees quick and easy access to all the necessary information – whether at the building yard or directly on the construction site.
With intuitive search functions and clearly structured content, teams can easily access relevant information and focus on what they do best: high-quality scaffolding work. In addition, Sebastian organizes special training courses to ensure that every employee knows exactly how to use the system efficiently.
By combining state-of-the-art technology and practical training, Sebastian Waack is transforming scaffolding into a sector that is not only safer, but also more efficient and future-proof.
Problem solving in scaffolding construction:
Simply put: rectify faults in scaffolding construction
Mistakes can happen when erecting scaffolding. That’s stupid because the same mistakes often happen again.
Sebastian Waack helps with this. He has tools that show when something is wrong. And these tools help to rectify the error.
But one tool alone is not enough. That’s why Sebastian brings the team together and shows everyone how to avoid mistakes.
Thanks to Sebastian, there are fewer mistakes when building scaffolding. And if an error does occur, it is quickly rectified. This makes scaffolding safer and better. Do you want that too?
Scaffolding is more than just erecting scaffolding. Sometimes errors occur, and if they are not corrected properly, they can happen again and again.
But with Sebastian Waack there is a solution. He has developed special methods that help companies not only to find errors, but also to rectify them permanently. This means that once a problem has been solved, it will not come back.
Its digital tools show immediately if something is wrong. And the best part? They help to rectify the error step by step.
But a computer program alone is not enough. That’s why Sebastian brings the whole team together and trains them. Everyone learns how to prevent problems and how to fix them quickly if they do occur.
With Sebastian’s help, scaffolding teams work better together, solve problems faster and ensure that errors do not recur. The result: safer and more efficient scaffolding construction. Are you ready to improve your scaffolding with Sebastian?
Clear communication in the scaffolding trade:
Good information for everyone in scaffolding construction:
Sometimes people don’t know exactly what to do when scaffolding is being erected. This can be dangerous.
Sebastian Waack helps with this. He has a system that allows everyone to get information quickly and easily. Everyone then knows how to build the scaffolding correctly.
He also shows the teams how the system works. In this way, errors can be avoided. With Sebastian’s help, everyone works better and more safely together.
Everyone in the team must know exactly how to erect scaffolding safely and correctly. However, if the information is not clearly communicated to everyone, mistakes can happen.
Sebastian Waack knows the problem and has the solution. It brings digital communication systems into play, which ensure that every employee understands exactly which quality standards must be met.
With real-time notifications, all team members are always up to date. There are also training sessions and reminders to ensure that no one misses out on important information.
But it’s not just about technology. Sebastian Waack meets with the teams, clarifies questions and makes sure that everyone understands what needs to be done. This ensures that quality standards always remain in focus and that the scaffolding trade is in top form. With a clear understanding and the right communication tools, scaffolding construction becomes safer, faster and better.
Continuous control in scaffolding construction:
Well controlled in scaffolding construction with Sebastian:
A good scaffold needs to be checked often. Some companies only realize mistakes very late and that can be expensive.
Sebastian has a good idea on how to do this better. He uses special computer programs that show immediately if there is a problem somewhere. This allows errors to be rectified immediately.
It also has programs that ensure that everything you need for building is always there.
But Sebastian knows that technology alone is not enough. That’s why he explains to the construction workers exactly how these programs work. And he shows them how important it is to always check everything. With Sebastian’s help, scaffolding construction becomes safer and fewer mistakes are made.
Stable and safe scaffolding requires regular and thorough quality checks. However, scaffolding companies often only discover defects once they have already intervened more deeply in the work process – a costly and risky situation.
But Sebastian Waack has the solution. Using modern monitoring systems, he ensures that the scaffolding is continuously checked. Special tools enable weak points or deviations to be identified immediately and rectified straight away.
In addition, real-time data enables immediate adjustment and optimization of work processes. There are even specialized systems that ensure that all the necessary materials and tools are always available.
But Sebastian doesn’t just rely on technology here either: he takes the time to train employees in the new technologies and raise awareness of continuous quality controls. With his expert knowledge and innovative systems, he ensures that scaffolding construction is not only more effective, but above all safer.
Other topics relating to the scaffolding trade
More details about the building blocks
Process documentation
Process documentation in the scaffolding trade: accuracy meets speed. Every action defined, every component taken into account. Architecture with foresight!
Digitization
Digitalization in the scaffolding trade: technology combined with craftsmanship. Every task digitally supported, every detail in the cloud. Experience modern building!
Inventory Management
Inventory & supply chain management in the scaffolding trade: organization meets precision. Every part counted, every delivery in flow. Seamless construction guaranteed!
Employee development
Employee & personnel development in the scaffolding trade: talent meets training. Every skill sharpened, every team synchronized. A strong future through strong teams!
Contact: I am looking forward to your message
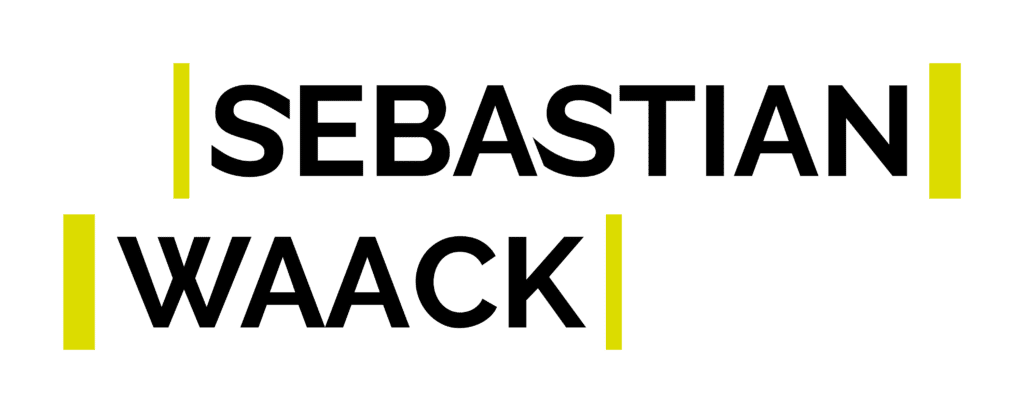
Your direct line to me.
I look forward to your message and will get back to you as soon as possible.
- Bremen & online via Zoom
- inquiry@sebastianwaack.de
- +49 (0) 176-414 862 64
FAQs
-
Quality management in the scaffolding trade refers to systematic measures to ensure the quality of products and services. The aim is to consistently fulfill customer requirements and strive for continuous improvement.
-
Effective quality management ensures the reliability and safety of scaffolding. It helps to gain customer confidence, reduce operating costs and strengthen the company’s market position.
-
Sebastian Waack can define quality standards, conduct internal training and implement control mechanisms to ensure compliance with these standards.
-
It minimizes errors, increases productivity, promotes customer satisfaction and creates a continuous improvement process within the company.
-
Depending on the size and complexity of the company, this can take several weeks to months.
-
After implementation, regular audits and reviews should take place to ensure the effectiveness of the system and identify potential for improvement.
-
Through continuous training, feedback loops and the integration of quality targets into the corporate strategy.
-
technology facilitates data collection, analysis and monitoring, resulting in more precise quality control and faster response times to problems.
-
Employees take pride in producing high-quality work. Effective quality management recognizes their efforts and promotes a positive working environment.
-
Start with an analysis of current quality standards, identify areas for improvement and consult experts like Sebastian Waack for customized solutions.
-
While some aspects can be managed internally, external expertise often offers deeper insights and specialized knowledge.
-
Some results, such as improved workflows, can be noticed immediately, while others, such as increased customer satisfaction, are more long-term.
-
There may be initial costs, but the long-term benefits in terms of more satisfied customers and more efficient processes often outweigh these expenses.
-
It is important to remain flexible, carry out regular reviews and make adjustments where necessary.
-
Quality management should be closely linked to the corporate mission and vision and anchored in all business areas to ensure consistent quality assurance.